So the original specification was that the bottom and sides of the hull be planked with strips of 1/4″ Okoume marine plywood. There were a couple of issues with this. First, it would have been really inefficient from a material perspective. The bulk of the strips need to be about 5′ long which, given that plywood comes in 4’x8′ sheets, means you’d be throwing away a huge amount of material. And this isn’t cheap stuff. Each sheet is about $100 and we would need something like 16 plank just the sides of the boat. The second issue is that there are some really tight bends in this thing, and torquing 1/4″ plywood into them would have been a very difficult task.
After a bit of discussion with Timm, I decided instead to plank the sides with three layers of 0.166″ thick, 4″ wide strips of western red cedar. Unfortunately, you can’t just go buy 4″x0.166″ WRC. What you can buy is rough sawn 8/4 lumber in 10′ and 12′ lengths. And that’s what we did. Then came the amusing step of converting the big lumber into small lumber.
To do that, we first surfaced the rough lumber and ripped the 8″ wide planks into 4″ wide planks. Here’s a shot of the surfacing process. I’ve got a Rojek 12″ jointer-planer that I picked up on Craigslist. It’s proven to be a great machine.

Then we resawed the 4″ wide planks into strips known as veneers that were about 0.20″ thick. Here’s the resaw operation. It’s not hard work, but it’s mind-numbingly repetetive.
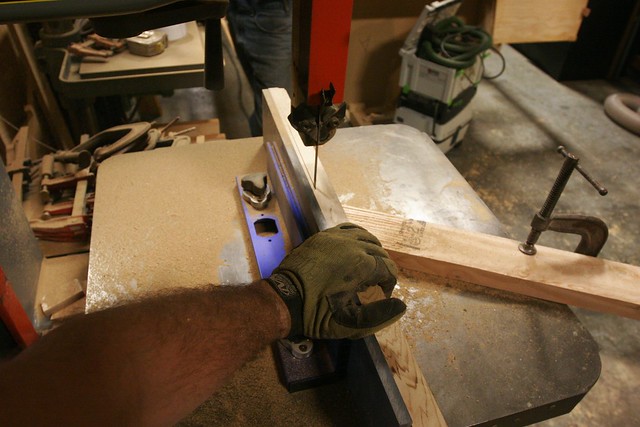

This is expensive wood – you’re looking at nearly $1000 worth of WRC in that stack – but it’s really the best approach to this part of the process. It’s also quite likely that using WRC saves money since we’re throwing less away. We shall see. For the time being, we’ve got more than enough to start planking the hull!
-Ben